PISTON RINGS
Piston rings are placed within the piston grooves along the outer diameter of the compression piston. The primary purpose of the piston ring is the create a dynamic, pressure-activated, seal between the piston and the cylinder to allow the compression operation to take place. CDI presents various piston ring designs various piston ring designs and materials, ensuring optimal sealing and ring longevity.
WEAR RINGS
The role of the wear ring is to provide a low-friction surface to carry the weight of the piston and prevent piston contact with the cylinder wall and reducing wear to the cylinder bore. CDI offers a variety of wear ring designs and materials, including polytetrafluoroethylene (PTFE) and bronze, which can be easily replaced for cost-effectiveness. These options help to ensure maximum wear ring longevity and efficient compressor operation.
PACKING RINGS
Pressure packing rings serve as dynamic, pressure-activated seals. The fundamental sealing ring comprises an assembly of two or more segment-cut rings that overlap at the joints, creating a seal. Garter springs maintain the segments' cohesion and contact with the piston rod during assembly and compressor downtime. CDI presents various pressure packing styles and materials to ensure optimal sealing and ring longevity.
VALVE COMPONENTS
CDI produces a wide selection of non-metallic valve plates and poppets for use in reciprocating compressors. CDI valve components are injection molded and machined to customer specifications to ensure excellent surface finish and flatness. These plates endure impact and fatigue loads when coming into contact with the valve seat, and harsh gas, liquids, and debris that can reduce the overall life of the valve. CDI manufacture valve plates, poppets, and buttons from a variety of non-metallic materials including PEEK, Nylon, and MT as well as more specialty polymers such as carbon filled PEEK blends.
OIL WIPERS
The primary purpose of the oil wiper is to prevent lubricating oil from the compressor frame from migrating along the piston rod and coming into contact with other critical sealing components within the compressor or mixing with the compressed gas. CDI offers various oil wiper designs in both metallic and non metallic materials to ensure optimal oil removal and wiper longevity.
PACKING CASE DESIGN
Packing case design and manufacturing are crucial for reliable and efficient reciprocating compressor operation. Packing cases house a series of packing rings and seal high-pressure gas from exiting the cylinder along the path of the piston rod. CDI offers pressure, intermediate, and wiper assemblies tailored for all reciprocating compressor applications, utilizing a wide material range, reliable ring design, and top-notch engineering. Design considerations include gas type, operating pressure, temperature, compressor size, and stroke.
PACKING CASE MANUFACTURING
CDI excels in creating high-quality reciprocating compressor packing cases to satisfy our customers' demanding requirements. Precision machining and collaborative robotic-assisted manufacturing underpin CDI's packing case production, ensuring resilience against operational stresses and pressures. Proper ring set installation and pressure testing are vital for compressor longevity and reliability.
SPRING ENERGIZED SEALS
The OptiSeal spring-energized seal is a reliable choice for use in volume pockets and actuators for reciprocating compressors. Its sealing lip and spring provide consistent sealing performance under harsh conditions, while its chemical resistance and low friction make it compatible with various gases and fluids. Easy installation and maintenance make OptiSeal an ideal option for demanding reciprocating compressor applications that require durability and reliability.
Hydrogen Compressors: The Green Powerhouse of the Future
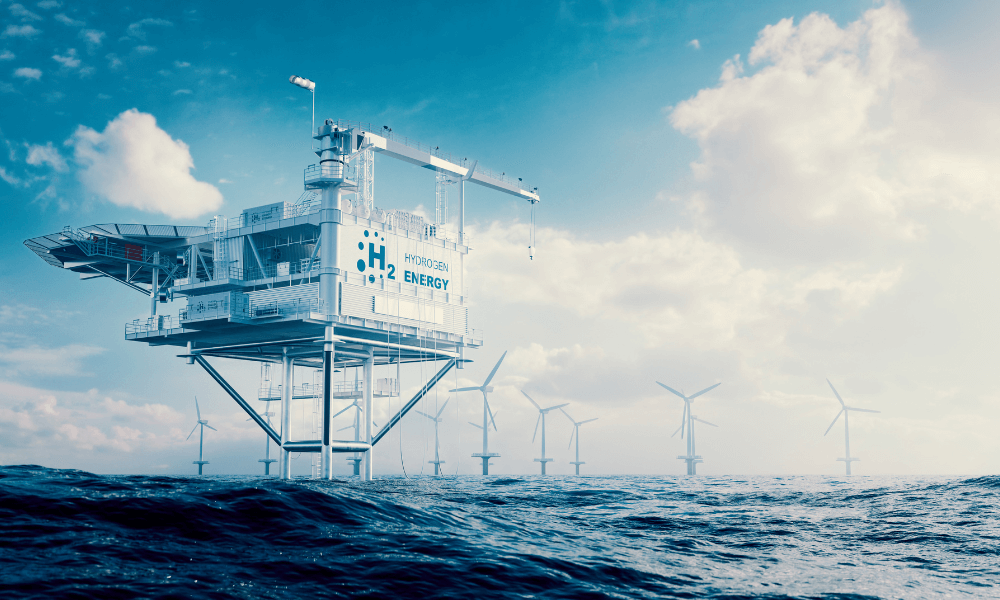
As we embark on a journey towards a greener and more sustainable world, hydrogen compressors emerge as the ultimate powerhouse for the future of clean energy. These cutting-edge machines harness the power of hydrogen, one of the most abundant elements in the universe, to deliver highly efficient and environmentally friendly energy solutions. Today, compressor manufacturers are partnering with CDI Products, leveraging our expertise in creating robust and durable components that can withstand the rigors of hydrogen compression. At CDI Products, we are paving the way for a new era of sustainable power generation by partnering with compressor manufacturers. Embrace the future today and join the hydrogen revolution, where innovation, efficiency, and eco-consciousness come together to create a brighter tomorrow.
Why Compressor Manufacturers Partner With Us
CUSTOM ENGINEERED POLYMER COMPONENTS FOR COMPRESSORS
Our comprehensive collection of high-performance polymeric materials, combined with our in-house engineering and design proficiency, provides our clients with an unmatched resource for converting sophisticated engineering materials into exceptional solutions. Our assortment of materials allows compressor manufacturers to boost dependability, augment efficiency, and achieve significant cost savings over the product's life cycle.
COMPRESSOR IMPROVEMENTS INCREASE COMPONENT DEMANDS
With roots dating back nearly 200 years, the reciprocating compressor industry has experienced significant advancements in both performance and reliability. As a result, the need for high-quality components in compressors has become increasingly crucial.
Reciprocating compressor efficiency and dependability have been bolstered through engineered polymeric and thermoplastic materials in critical sealing components. As compression boundaries continue to be pushed, more sophisticated materials and inventive seal designs are needed to meet these growing demands.
EXPANSIVE POLYMER MATERIAL SELECTION
Opting for meticulously chosen engineered polymer materials allows for an improvement in compressor performance without compromising reliability. CDI's selection of materials boasts some of the most advanced engineered polymer options currently available for use in piston rings, wear bands, packing rings, wiper rings, and spring-energized seals.