Elastomers Made for Extreme Environments
Considering the range of polymeric compounds used in the various industries we serve, elastomeric materials can be among the most challenging, and sensitive materials when manufacturing products. To ensure materials are capable of surviving a range of performance and operating scenarios, from High-Pressure High-Temperature (HPHT) environments, Rapid Gas Decompression (RGD), or severe chemical attacks, materials must be compounded and selected after evaluating a range of critical factors prior to the design process.
Our depth of experience allows us to produce materials with minimal batch variation and consistent quality. Our molding processes – compression, transfer, and injection – satisfy both low and high-volume production.
HEAT, CORROSION AND OTHER POTENTIAL THREATS
If materials are chosen improperly, bottom-hole temperatures (BHT) escalating to 400°F can pose an immediate threat to the integrity of seal materials, making the application susceptible to failure. Aggressive chemical environments such as hydrogen sulfide, paraffin inhibitors, acids, and bromides accelerate critical component corrosion.
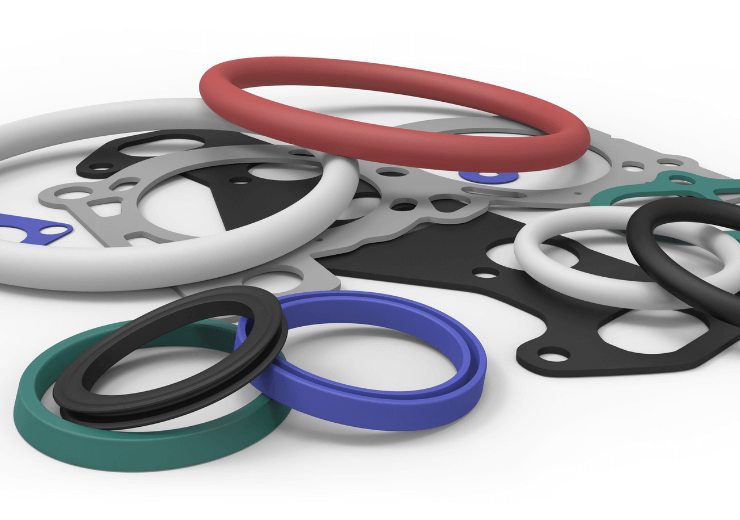
High levels of CO2, methane or other compressible fluids create rapid gas decompression (RGD), one of the leading causes of seal failure. Therefore, selecting elastomers with the correct resilience and durability is imperative to withstand these harsh environments and maintain operational efficiency.
ARYLAST™ IS A PREMIUM-QUALITY MATERIAL WITH A WIDE SPECTRUM OF USES ACROSS VARIOUS INDUSTRIES AND APPLICATIONS
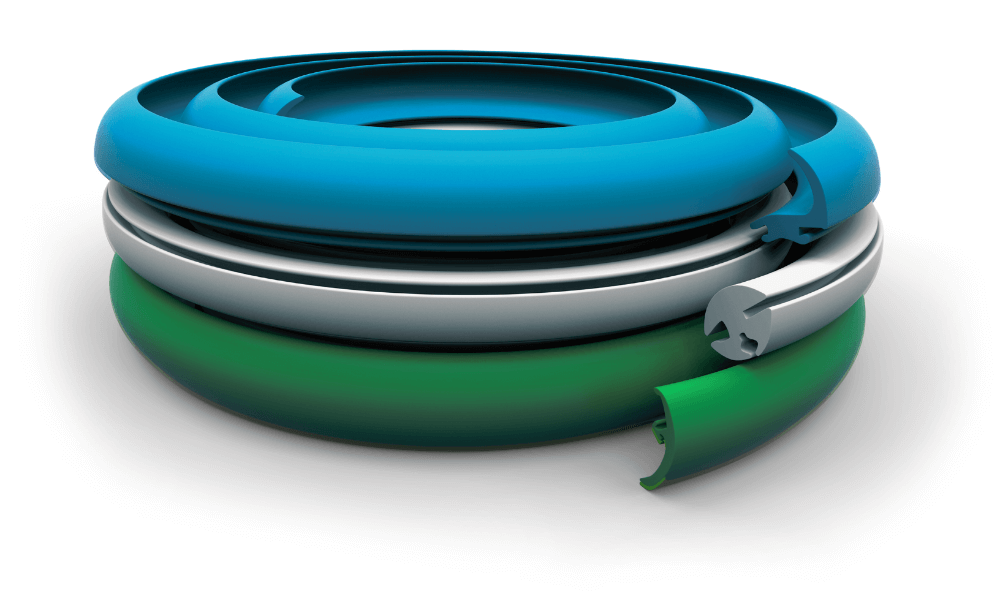
Arylast™, developed by CDI, is an advanced material range for various industries. The line includes engineered elastomers like Nitrile (NBR), Hydrogenated Nitrile (HNBR), Fluorocarbon (FKM), Ethylene Propylene Diene Monomer (EPDM), Fluorosilicone (FVMQ), and Perfluoroelastomer (FFKM). NBR, useful with mineral oils, operates at 80°F to +250°F. The improved physical and thermal properties of HNBR are of benefit in harsh well services and other applications where NBR is not quite enough. HNBR works well from -40°F to +320°F service temperatures. FKM, known for its outstanding resistance to chemicals and thermal degradation, works at -40°F to +400°F (short term to +500°F). FVMQ, used in military systems (useful for its low temperature flexibility), functions from -76°F to +392°F. FFKM, (known for its unmatched resistance to most of chemicals and high resistance to thermal degradation) found in aircraft engines, operates at temperatures up to -13°F to +620°F. Lastly, EPDM, used with brake fluids, operates at -65°F to +350°F.
Elastomer Application Insights
NBR (Nitrile Rubber)
Nitrile rubber elastomer is the workhorse of both the fluid power, and oil and gas industries, due to good oil and fuel resistance. NBR compounding is very diverse, due to the variety of polymer types and cure methods available. NBR is a copolymer of acrylonitrile (ACN) and butadiene. A high percentage of ACN reduces swell in oil and fuel. The drawback is that the low temperature service capability is reduced, thus a compromise is required. Sulfur vs. peroxide cure must be evaluated based on service requirements and cost effectiveness.
Service - NBR is suitable for most petroleum product applications. Other areas of use are in water, glycols, and silicones. Resistance to high pressure CO2 and methane require high modulus compounds to resist explosive decompression. NBR is not recommended for service in concentrated acids and, bases, ketones, esters, bromides, and steam. NBR compounds are generally suitable for -40 to +250°F service depending on the application and seal geometry.
HNBR (Hydrogenated Nitrile Rubber)
Hydrogenated Nitrile Rubber is a high-performance class of nitrile polymer. Compounds of HNBR retain the oil and fuel resistance of regular nitriles, but also exhibit improved physical and thermal properties. These improvements are the result of reducing or eliminating unstable double bonds in the polymer backbone. This reduction of double bonds or hydrogenation provides improved chemical resistance over regular nitriles.
Service - HNBR is generally suitable for all regular nitrile applications. The improved physical, chemical and thermal properties of HNBR are of benefit in harsh well services and other applications, where nitrile is not quite suitable. HNBR is not recommended for service in strong acids, ketones, esters, and bromides. HNBR compounds are generally suitable for -40°F to +320°F service depending on the application and seal geometry.
EPDM (Ethylene Propylene Diene Monomer Rubber)
Ethylene Propylene Diene Monomer elastomer is used in applications that require good aging properties, such as in heater / radiator hoses, exterior weather, and water seals. In the fluid power industry, EPDM offers excellent resistance to water based hydraulic fluids. In the oil and gas industry EPDM is used in applications involving steam, such as enhanced recovery and geothermal energy. The non-polar structure of the polymer can be altered to give a wide range of properties and uses. The fully saturated form Ethylene Propylene (EPM) must be peroxide cured. A third monomer, diene can be added to the polymer to create EPDM, this facilitates sulfur curing.
Service - EPM & EPDM is suitable for most water, steam, alcohols, ketones, phosphate esters. Other areas of use are in non-petroleum-based fluids such as glycol and silicone based hydraulic fluids. EPM & EPDM generally offer good resistance to acidic and caustic solutions. EPM & EPDM is not recommended for service in petroleum oils & fuels, diester fluids, aromatic hydrocarbons. EPM & EPDM compounds are generally suitable for -60°F to +350°F service depending on the application and seal geometry.
FEPM (Tetrafluoroethylene Propylene Rubber)
FEPM is a high-performance class of fluorocarbon & olefin co-polymers, the best known being the Aflas® brand of Tetrafluoroethylene Propylene. Compounds of FEPM offer good oil and chemical resistance, along with excellent thermal properties. The notable improvements over FKM polymers for oilfield applications are resistance to strong acids and bases, highly concentrated sour gases, and steam. Newer FEPM-2 polymers based on ethylene, TFE and PMVE offer increased resistance to hydrocarbons.
Service - FEPM is widely used in oilfield and chemical applications. FEPM resists oil, amine corrosion inhibitors, H2S, CO2 and CH4, which are encountered in harsh well service. FEPM is recommended for service in acids, bases, hydraulic fluids, brake fluids, steam, alcohols, ozone, and gamma radiation. FEPM is not recommended for service in toluene, ethers, ketones, acetates, and halo hydrocarbons. FEPM compounds are generally suitable for +30°F to +450°F service depending on the polymer grade, application, and seal geometry.
FKM (Fluorocarbon Elastomers)
Fluorocarbon elastomer is a high-performance polymer. Compounds of FKM offer good oil and chemical resistance, along with excellent thermal properties. FKM can be divided into several types based on their chemical composition. Two major types of polymers exist: FKM copolymer of vinylidene (VDF) and hexafluoropropylene (HFP) (Type 1) and FKM terpolymer of VDF, HFP, and tetrafluoroethylene (TFE) (Type 2). The higher fluorine content in the terpolymer offers increased chemical resistance at the expense of low temperature capability and compression set. FKM (Type 3), which offers excellent low temperature flexibility, contains VDF, TFE, and perfluoromethylvinylether (PMVE).
Service - FKM is widely used in oilfield and chemical applications. FKM resists oil, H2S and CH4, which are encountered in harsh well service. FKM is recommended for service in acids, hydraulic fluids, aromatic hydrocarbons and ozone. FKM is not recommended for service in ketones, amines, methanol and steam. FKM compounds are generally suitable for -25°F to + 400°F service, functional temperature ranges are dependent on the application, gland design and seal geometry.
FFKM (Perfluoroelastomers)
Perfluoroelastomer elastomer is a fully fluorinated high-performance polymer. Compounds of FFKM offer more chemical and thermal aging resistance over traditional FKM and FEPM compounds. Due to the fully fluorinated polymer structure, these polymers offer the broadest chemical resistance of any seal material, except PTFE. Due to the very high material cost of FFKM polymer, use is generally restricted to critical applications.
Service - FFKM is widely used in oilfield and chemical applications. FFKM resists oil, amines, H2S and CH4, which are encountered in harsh well service. FFKM is recommended for service in acids, bases, hydrocarbons and ozone. FFKM compounds are suitable up to 450°F, while triazine cured FFKM can resist temperature as high as 620°F.