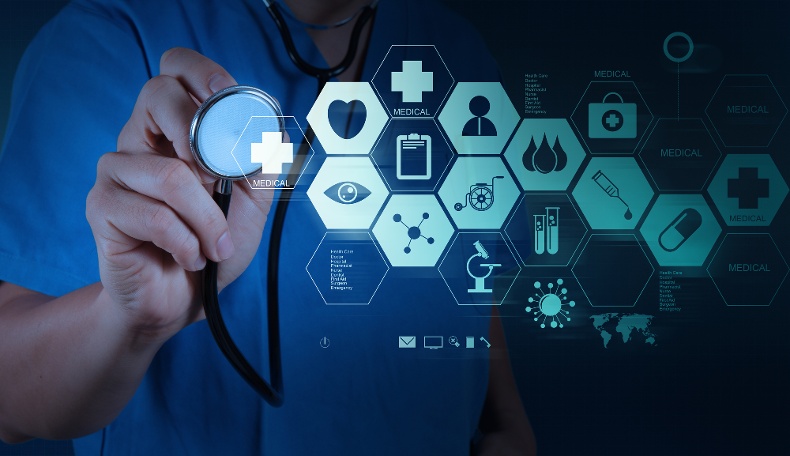
The Top 6 Thermoplastics Trusted in the Healthcare Industry
Posted by CDI Products on Sep 27, 2021
Plastics have been a major catalyst in the transformation of healthcare. The early healthcare industry functioned with basic components like glass intravenous (IV) bottles, rubber tubing, and metal operating room devices.
Plastics development in the 1930s, 1940s, and 1950s paved the way for new materials, such as polyvinyl chloride (PVC) for IV bags and tubing, silicone tubing for catheters and balloons, polyolefins for trays and bottles, and fluoropolymers for IV catheters.
As new materials were discovered and new products and devices were available, the overall health of the population vastly improved. Many of these new materials were used for single-use goods that could deliver a more reliable level of physical separation, sanitation, and patient safety that:
- Reduced the rate of infectious diseases
- Improved pain management and increased patient comfort
- Delivered life-sustaining medications and vaccines
- Increased life expectancy around the world
Thermoplastics Go the Distance
With improvements in medical procedures and equipment, biomedical technologies, and major pharmaceutical breakthroughs, plastic has established itself as one of the few adaptable materials capable of adapting to the industry’s dynamic nature and constant evolution.
While polymers have been used in the healthcare industry for decades, more recently industry leaders are embracing the benefits of using specialty compounds and thermoplastics in medical, biomedical, and pharmaceutical applications. Beyond single-use plastics, higher performance polymers, medical-grade plastics, and thermoplastics present long-term value to patients and to healthcare as a whole.
Determining the Right Material
Applications in the healthcare industry, and medical devices in particular, have some demanding requirements for thermoplastic materials that are unique to this arena. Understanding thermoplastics sterilization compatibility, anti-static range, creep and corrosion resistance, and biocompatibility is essential for selecting the right material for use.
Determining the right thermoplastic for the application requires a deep understanding of the material characteristics, its performance over time, and the potential environmental exposure. We’re essentially asking, “In what conditions must the material endure, and what must survive around the material?”
Some of the most common environmental conditions to consider include applications that require:
- Contact with internal body tissue or fluids
- A higher level of sterilization
- Medical device materials being in the medication flow path
The Top 6 Thermoplastics
Although many thermoplastics have value to the medical, biomedical, and pharmaceutical field, here are the six most readily used materials trusted by healthcare professionals worldwide.
- Ultra-High Molecular Weight Polyethylene (UHMW-PE) is a medical-grade plastic with high-impact strength, good wear and abrasion resistance, excellent chemical resistance, and outstanding low temperature properties.
- Engineers choose UHMW-PE because it is produced from premium resins in accordance with ASTM specification F648 and international ISO standards 5834-1 for surgical implants and medical devices.
- Healthcare markets that regularly use UHMW-PE include sports medicine, orthopedics, medical device, drug delivery, pharmaceutical, cardiovascular, neurological, and diagnostic medicine.
- Polyether Ether Ketone (PEEK) is a unique engineering thermoplastic that also offers excellent chemical compatibility, low susceptibility to stress cracking, clinically proven biocompatibility, high dimensional stability, and good electrical insulation.
- Engineers choose PEEK because it is easy to machine and it has excellent mechanical strength and impact properties.
- Healthcare markets that regularly use PEEK include spine, sports medicine, cranial, orthopedics, medical device, drug delivery, pharmaceutical, cardiovascular, neurological, and diagnostic medicine.
- Acrylic, the common name for polymethyl methacrylate (PMMA), is a medical-grade thermoplastic used in the manufacture of medical devices and medical implants such as intraocular lens implants, bone cement, and cranial implants.
- Engineers choose acrylic for medical devices requiring impact strength, chemical resistance, biocompatibility, and clarity.
- Healthcare markets that regularly use acrylics include drug delivery, pharmaceutical, cardiovascular, neurological, and diagnostic medicine.
- Acetal Copolymer (Polyoxymethylene) is a medical-grade thermoplastic with high mechanical strength, rigidity, and dimensional stability. It delivers good sliding characteristics and excellent wear resistance, as well as low moisture absorption.
- Engineers choose Acetal Copolymer due to its good dimensional stability and particularly good fatigue strength, as well as excellent machining ability, making it a highly versatile engineering material, even for complex components.
- Healthcare markets that regularly use Acetal Copolymer include spine, sports medicine, orthopedics, medical device, drug delivery, pharmaceutical, cardiovascular, neurological, and diagnostic medicine.
- Polypropylene (PP) is a thermoplastic manufactured by the catalytic polymerization of propene. PPs are universal standard medical-grade plastics with well-balanced properties providing excellent chemical resistance, high purity, low water absorption, and good electrical insulating properties.
- Engineers choose medical-grade polypropylenes because they also offer excellent dimensional stability, machinability, and the ability to withstand sterilization from steam autoclaving.
- Healthcare markets that regularly use PP include spine, sports medicine, orthopedics, medical device, drug delivery, pharmaceutical, cardiovascular, neurological, and diagnostic medicine.
- Polyphenylene Sulfide (PPS) is a high-temperature thermoplastic polymer that is very chemically resistant with amazing mechanical strength, even at temperatures above 200°C (392°F), with low susceptibility to creep.
- Engineers choose PPS due to its low water absorption, good dimensional stability, and excellent electrical properties.
- Medical markets that regularly use PPS include medical device, drug delivery, pharmaceutical, cardiovascular, neurological, and diagnostic medicine.
What Does the Future of Plastics Look Like for Healthcare?
With all the benefits plastics bring to an industry founded on the principle to do no harm, there is also the question around the impact of plastics on our environment. As a global community, we are all looking for ways to reduce our reliance on single-use plastics.
With their inherent reusability and recyclability, thermoplastics may open doors for new ways to maintain patient safety without unnecessary waste. Scientists and chemists around the globe are researching innovations in thermoplastics, including fully biodegradable polymers suitable for medical applications.
Plastics have a history of real benefits to the healthcare industry and in the global health of people around the world. We look forward to being a part of the next evolution in plastics and have a hopeful eye on the future ahead.
Topic: engineered thermoplastics, thermoplastics, healthcare thermoplastics