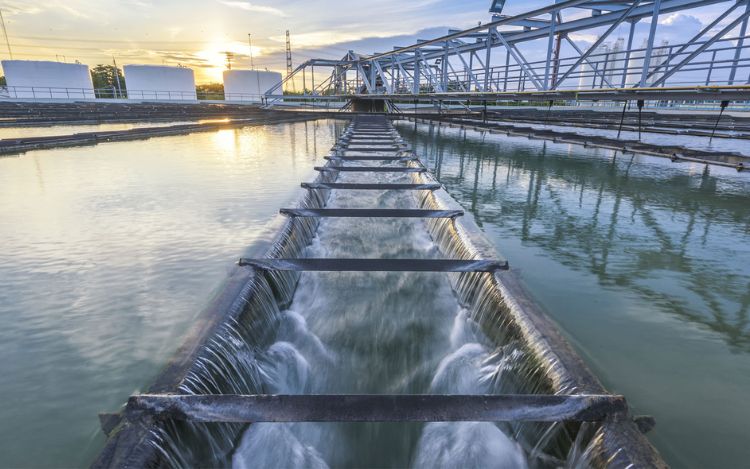
How Fluid Cleanliness Impacts Seal Performance
Posted by CDI Products on Jan 17, 2023
Seals – Such as O-rings, gaskets, and hydraulic seals – play a critical role in the efficiency and productivity of rotating and moving machine assemblies. They are also one of the most susceptible components to fail in the extreme and harsh conditions in which they’re expected to perform.
Problems with installation, surface finish, and operating conditions are just a few of the common ways seals fail. But don’t underestimate the importance of fluid cleanliness.
All fluids contain some level of impurities. In fact, research shows that up to 70% of all system failures are a result of contamination.
Contamination increases wear, abrasion, and impact damage to seals. It also affects the fluid film under the seal. Companies that depend on lubricating and hydraulic fluids should keep those fluids clean and performing at peak levels for as long as possible.
Types of Fluid Contamination
- Particles that were already present in the system’s fluid before being introduced (through lack of pre-filtering)
- Dirt, sludge, water, dust, and oil that are introduced through the rod/piston seals, component seals, or improperly fitted covers
- Ingressed particles that draw or create larger particles that chafe against moving parts, causing abrasion, corrosion, cavitation, erosion, and fatigue
- When other particles in a fluid undergo a chemical reaction due to catalytic contamination from water, air, or heat
Additional types of contamination include:
- Lint
- Machine burrs
- Rust
- Sand
- Metallic shavings
- Cleaning rag fibers
- Weld spatters
Sources of Fluid Contamination
Every lubrication system contains particulate contamination. The level of contamination varies depending on the type and efficiency of the filters used, as well as the system’s design, age, and operating environment. Despite recent advancements in cleaning techniques, dirt particles can be found in all system components – including pumps, valves, pipes, and hoses – even before the system is put together.
Contamination comes from several sources, such as:
- Particles left in the system during manufacturing
- Oil that’s not properly filtered before it enters the system
- Particles and condensing water that pass through an opening or bypass the seals
- Particles created by wear on one or more components
In turn, component wear is brought on by:
- Abrasion: When lubricated surfaces come into contact with one another or lubricated surfaces are harmed by clearance-sized particles
- Adhesive wear: Material is eroded from one surface
- Fatigue: Causes an elastic deformation of a component’s surface
- Erosion: Created by the abrasive slurry that forms when silt-sized particles in a fluid corrode surfaces
- Cavitation: Caused by the pressure-induced collapse of vapor or air bubbles, which corrodes metal components
- Corrosion: Generated when hydraulic oil is broken down by heat or water, which produces chemical byproducts like acids that attack some metals
It’s critical to recognize seal contaminants and their sources before they develop into more serious problems. No matter how wear happens, contamination by particles inside the system (internal) or those that manage to get inside (ingress) can be reduced or avoided with the right seals.
How Sealing Components Can Affect Contamination
Wear rings, hydraulic seals, wiper seals, and static seals are the four main subcategories of seals used in hydraulic systems. Each of these components, when used properly, can help to prevent contamination. However, when not designed or installed properly, can themselves become a source of contamination.
1) Wear Rings
Most hydraulic sealing configurations include wear rings. They serve to prevent metal-to-metal contact by absorbing transverse pressures and providing the physical separation needed to prevent damage. If wear rings are not replaced at proper maintenance intervals, metal touch-off can occur creating contaminants that could prove catastrophic to seal integrity.
2) Hydraulic Seals
The primary seals which allow for proper hydraulic systems to function are the hydraulic seals. These seals depend on clean hydraulic oil to seal properly. Damage to critical sealing surfaces from contaminants can cause leaks to the outside environment and ultimately premature failure.
3) Wiper Seals
Wiper seals have a scraping lip which faces towards the exterior environment. This lip serves to stop contamination such as dirt, dust, and water from entering and mixing with the sealing fluid.
4) Static Seals
Most hydraulic systems employ static seals which seal against two or more non-moving surfaces. These seals can themselves become a source of contamination when over-pressurization or temperature extremes result in seal damage, causing small pieces of seals to mix into the hydraulic fluid.
The Bottom Line
Seals can be found in nearly every application and industry, including aerospace, general industrial, water treatment, and oil and gas – each of which presents its own environmental challenges, such as extreme temperatures, high pressures, and aggressive media.
If sealing components are improperly designed or maintained, they could fail, and their ability to sustain lubrication, exclude contaminants, or separate media is at risk. Clean fluids are paramount to the healthy operation of mechanical equipment to ensure minimum wear, maximum equipment life, optimal efficiency, and ultimately reduced operating costs.
Topic: static seals, seals, fluid cleanliness, fluid contamination, wiper seals, wear rings, hydraulic seals