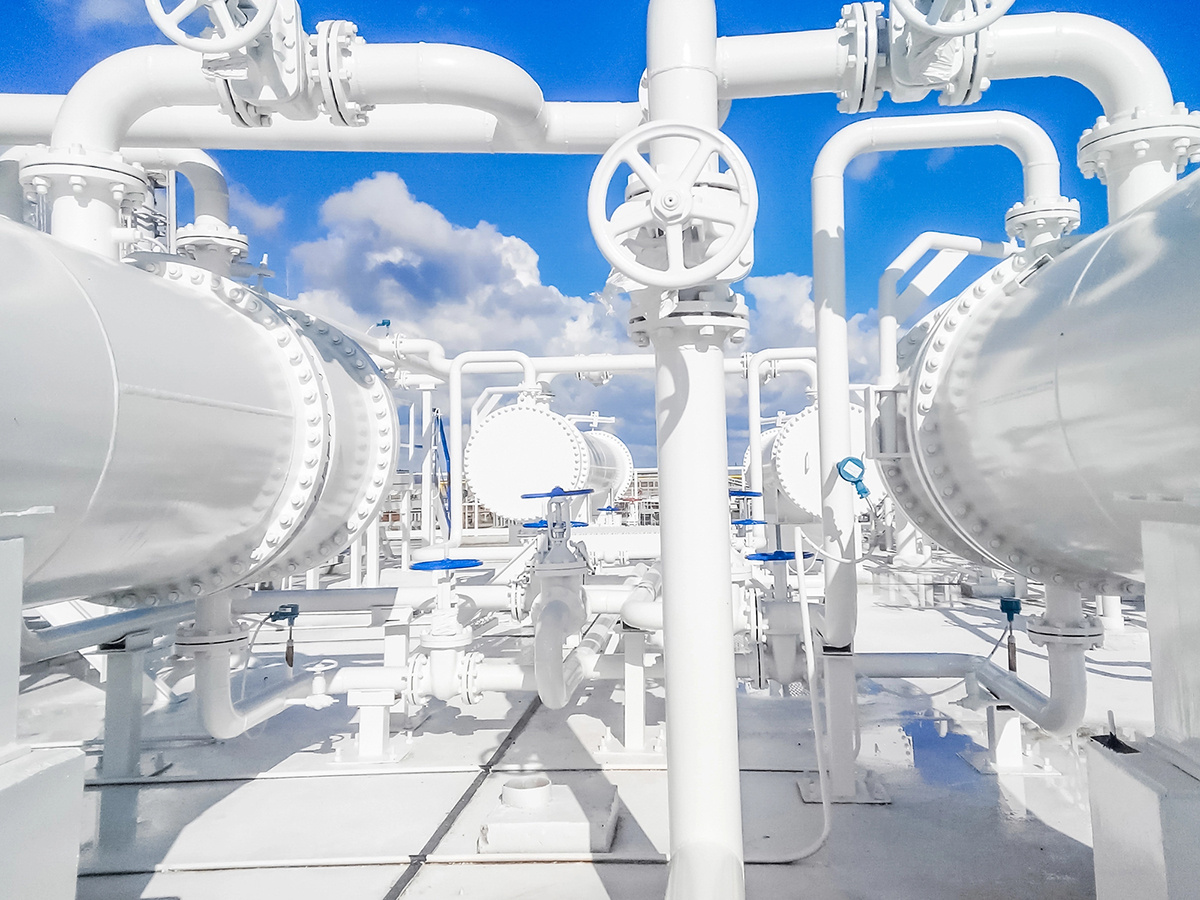
Enhancing Fugitive Emissions Control in API Valve Systems through Advanced Sealing Solutions
Posted by CDI Products on Aug 09, 2024
Abstract:
Fugitive emissions from industrial valve systems pose significant environmental and regulatory challenges, particularly in the oil and gas, chemical processing, and petrochemical industries. Addressing fugitive emissions requires robust sealing solutions that meet stringent leakage standards outlined by organizations such as the American Petroleum Institute (API). In this technical blog, we examine the importance of fugitive emissions control in API process valves and explore advanced sealing solutions aimed at minimizing emissions while ensuring operational reliability and compliance.
Introduction
Fugitive emission refers to the inadvertent and undesirable release, leakage, or discharge of gases or vapors from equipment or facilities that contain pressure, or from various components inside an industrial operation. This can include valves, piping flanges, pumps, storage tanks, compressors, and so on. Fugitive emission, more commonly referred to as leak or leakage, denotes the unintended release of these substances or gases. Emissions that are not accounted for during the design phase of equipment and components are referred to as "fugitive."
Efficiently preventing and mitigating leaks is of utmost importance in industrial settings to ensure safety, comply with environmental regulations, and maintain operational efficiency. Leakage from valve packing, seals, and gaskets can result in significant emissions of volatile organic compounds (VOCs) and hazardous air pollutants (HAPs), leading to regulatory violations, environmental impact, and public health risks. These impacts and risks are why proper sealing solutions are not only important for original equipment manufacturers (OEMs) and service providers, but to regulatory agencies around the world.
Regulatory Landscape and Standards
Ever since the U.S. Clean Air Act was implemented in 1963, the U.S. Environmental Protection Agency (EPA) and individual states have been imposing stricter consent decrees on fugitive emissions from industrial facilities. Numerous companies have successfully implemented Leak Detection and Repair (LDAR) programs, while industry groups have dedicated their efforts to assisting member companies in reducing valve emissions. In recent times, there has been a shift towards adopting a proactive and preventative approach in LDAR, moving away from the traditional repair mindset. This new approach emphasizes valve design and the achievement of low emissions (Low-E) performance at the manufacturer level. Regulatory agencies, such as API, ISO, MESC, BSI, JIP33, and TA-LUFT, have established stringent regulations and standards to limit fugitive emissions from industrial sources. API valve systems, designed to control fluid flow in process piping, play a pivotal role in fugitive emissions control. The API has developed guidelines, such as API Standard 622 for type testing of process valve packing for fugitive emissions, to ensure compliance and performance verification of sealing solutions in API valve systems.
Currently, there are three widely used methods for evaluating the emissions criteria of API valves and packings:
- API 622 Type Testing of Process Valve Packing for Fugitive Emissions - This specification replaces the need for a valve and the uncertainties associated with a specific valve by utilizing a standardized test fixture. Through the utilization of a test fixture and a predetermined set of conditions, it is possible to assess different packing sets from multiple manufacturers in a consistent manner to benchmark relative performance.
- API 624 Type Testing of Rising Stem Valves Equipped with Graphite Packing for Fugitive Emissions - This test standard is designed to assess the low emissions capability of a valve throughout an accelerated life cycle. It aims to evaluate the performance of the valve itself, rather than solely focusing on the packing.
- API 641 Type Testing of Quarter-turn Valve for Fugitive EmissionsThe type test for quarter turn valve designs evaluates the low emissions performance over an accelerated life cycle, encompassing a wide range of designs, temperature ratings, and sealing components.
Challenges in Fugitive Emissions Control
There are several challenges to overcome when it comes to achieving effective fugitive emissions control in API valve systems:
-
High Temperatures and Pressures: Valves operating in high-temperature and high-pressure environments require sealing solutions that can withstand extreme conditions without compromising performance.
-
Dynamic Operating Conditions: Valve systems subjected to frequent cycling, temperature fluctuations, and pressure variations present challenges for sealing integrity and longevity.
-
Regulatory Compliance: Meeting stringent emissions standards and testing requirements outlined by regulatory agencies and industry organizations necessitates reliable and verifiable sealing solutions.
-
Gas Permeation: Due to the small molecule size of fugitive emission gases, most sealing materials used in high-temperature applications cannot effectively prevent leakage with standard engineering practices. Consequently, this results in increased levels of gas permeation and compromised seal integrity.
Advanced Sealing Solutions for Fugitive Emissions Control
There are several advanced sealing solutions available to tackle the challenges associated with fugitive emissions control in API valve systems:
-
Low-Emission Packing: Engineered packing materials, such as expanded graphite, PTFE (polytetrafluoroethylene), and braided carbon fiber, offer low-emission performance while maintaining sealing integrity under high pressures and temperatures.
-
Gaskets: Graphite or PTFE based Spiral-wound, camprofile, or corrugated gaskets as well as flexible graphite and PTFE sheet gaskets provide reliable sealing solutions for flanged connections in API valve systems, offering chemical resistance, thermal stability, and conformability to irregular flange surfaces.
-
Pressure Seals: Graphite pressure seals with anti-extrusion devices are highly effective in sealing fugitive emissions. These seals provide a reliable barrier against gas and liquid leaks, ensuring environmental safety and regulatory compliance. The anti-extrusion devices prevent the seal material from being forced out under high pressure, enhancing seal longevity and efficiency. As a result, these seals are widely used in industries where maintaining a tight seal and preventing emissions are crucial.
-
Live-Loaded Packing Systems: Live-loaded packing arrangements incorporate spring-loaded mechanisms to maintain consistent packing compression, reducing the risk of fugitive emissions due to packing relaxation or wear.
-
Bellow Seals: Bellow seal valves offer effective fugitive emissions control in valve stem applications, providing a flexible barrier against leakage while accommodating dynamic movements and temperature variations.
Implementation Considerations and Best Practices
When choosing and implementing sealing solutions for controlling fugitive emissions in API valve systems, it is important to keep in mind the following considerations and best practices:
- Compatibility with Process Fluids: Ensure compatibility of sealing materials with process fluids, temperature ranges, and chemical environments to prevent degradation and leakage.
- Performance Testing and Certification: Verify compliance with industry standards, such as API 622, through type testing and certification of sealing solutions to demonstrate emissions performance and reliability.
- Maintenance and Monitoring: Implement proactive maintenance programs to inspect, adjust, and replace sealing components as needed to minimize the risk of fugitive emissions and ensure continued compliance with regulatory requirements.(If you are interested to learn more about Maintenance, Monitoring and proper sealing techniques, you may want to read our blog: Industrial Sealing Techniques: Mitigating Fugitive Emissions
Conclusion
Efficient management of fugitive emissions in API valve systems is crucial for safeguarding the environment, meeting regulatory requirements, and maintaining operational reliability in industrial facilities. Advanced sealing solutions, including low-emission packing, PTFE or graphite-based gaskets, bellows seal valves, and live-loaded packing systems, offer reliable and effective means of minimizing emissions while ensuring sealing integrity and performance under demanding operating conditions. Through the application of industry-leading techniques and cutting-edge sealing technologies, various sectors can make substantial strides in reducing fugitive emissions. This not only promotes sustainability, safety, and environmental responsibility but also enhances their standing in the global marketplace.
Wrap-Up:
If you are looking for quality polymer or flexible graphite parts for your valve systems, you can turn to our experts to serve your toughest challenges. For over 40 years, our experienced engineers have designed and manufactured components for a variety of valves: butterfly, ball, gate, globe, check, control, and pressure relief. CDI products and solutions help customers achieve long-term value through extended wear, improved performance and operating range, greater reliability, and engineering assistance to improve manufacturability. We take cost, quantity, load capacity, temperature, fluid media, and stem & housing materials into consideration to match the best valve component to the performance environment. We manufacture a variety of valve components, including:
- Custom-engineered stem seals and packing
- Thermoplastic and elastomer valve seats
- Bearings and thrust washers
- Body to Bonnet Seals
- Pressure seals
- Over-molded/lined PFA (Teflon®) components
- Custom Machined, Molded, or Formed Parts
Topic: valves, fugitive emissions, sealing solutions